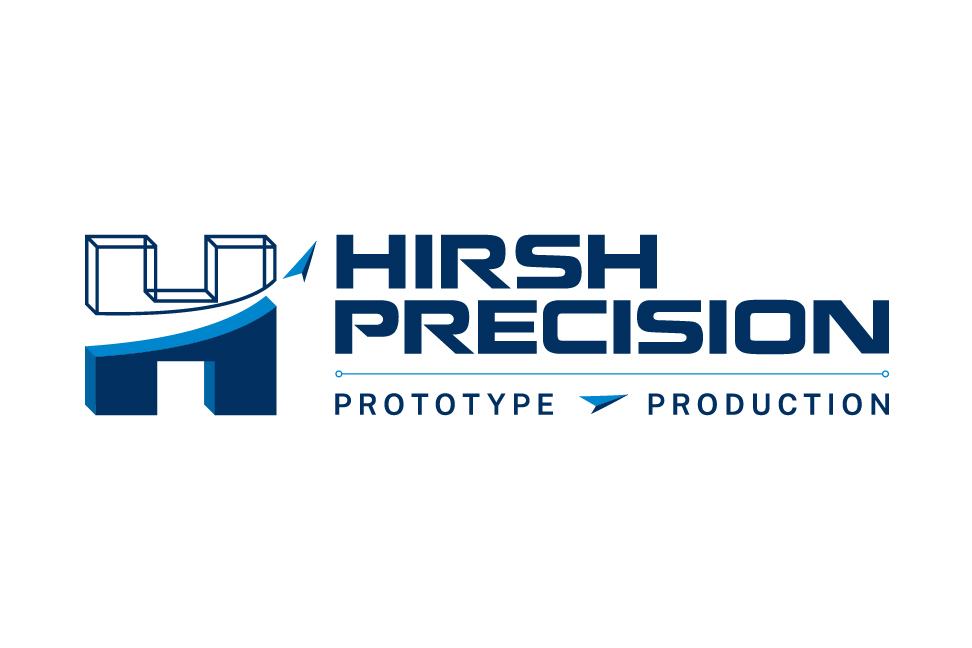
Solving Productivity Challenges with Automation
Hirsch Precision improves productivity with Fastems automation.
Since its foundation in 1980, Hirsch Precision has been dedicated to providing on-time, high-quality products and manufacturing services, while also continuously improving and conducting business with integrity. Hirsch supports the healthcare sector by manufacturing critical components for medical equipment used in hospitals.
Starting Ahead with Okuma Machines
Hirsch has always made it a mission to invest in innovative technologies to improve productivity on their shop floor. Their first ever Okuma machine was an LC10 installed in 1981, and since then, they have had 16 Okuma machines. From the beginning, Hirsch appreciated Okuma’s dedication to rigidity and durability, both of which play a large role in the ROI for the company and the quality and precision of the parts they manufacture.
Automating with Fastems
What initially drew Hirsch Precision to Fastems was their intentional investments in software that can schedule and monitor the machines on the shop floor. Fastems’s Manufacturing Management System (MMS) integrates production planning, production resources, and machinery into a single software that manages your entire CNC production. Previously, Hirsch had no management software and had been running multi-pallet machines. Combining Fastems’s MMS and pallet handling systems with their Okuma machines gave Hirsch three differentiators.
First, the scheduling system that Fastems provided for their operation enabled a different level of productivity that can’t be achieved with a multi-pallet machine alone. Secondly, utilizing MMS allowed them to accomplish shorter lead times with fewer setups, raising the overall productivity of their operation. Lastly, with a stable process, Hirsch could run unattended machines at levels they were previously unable to execute.
Increase Your Productivity with Automation
From low-volume to high-mix work, all productions can automate. President of Hirsch Precision, Peter Doyle, said of their automation journey, “We’re not a high-volume shop, and it was the scheduling system and the way that this multi-pallet system was arranged that allowed us to dedicate only one pallet to a particular item and still gain the advantages as if we had ten pallets dedicated to an item. We have not needed a high volume to realize the benefits [of automation].”
No matter your operation or application, the opportunity to automate is always present. With a partner like Hartwig, you receive the support and expertise you need to optimize your shop floor and easily set up and learn to operate your new automation systems. Learn more about how Hartwig can help you improve your productivity and the automation solutions we provide, and reach out to Hartwig’s resident automation expert Rick Spencer to create your tailored implementation plan today.
Ready to talk with a machine tool expert?
Your Hartwig representative can help connect you with the solution that will power your business’s next big innovation and efficiency.