Additive Manufacturing Led to Innovations that Improve Workflows And Life-Saving Technology for Patients
Hartwig, CoreLink Surgical, and EOS partner to bring game-changing technology for spinal implants to market
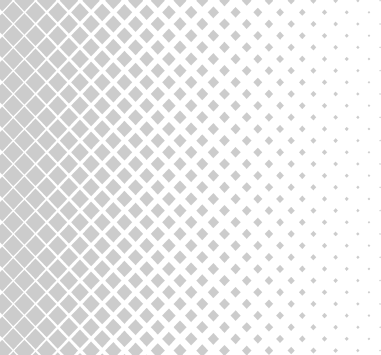
The Customer
There are quite a few advantages of 5-Axis machining, particularly to machinists and skilled operators. Namely, they don’t have to spend an entire day chasing accurate measurements. The integrated controls ensure greater accuracy when it’s running, regardless of what the ambient temperature is when it’s running.
Okuma 5-Axis machinery has provided that, and more, for a long-time partner and client of Hartwig, Homeyer Precision Manufacturing, providing game-changing business innovations that increased not just accuracy, but also helped them attract a new class of professionals to their workforce.
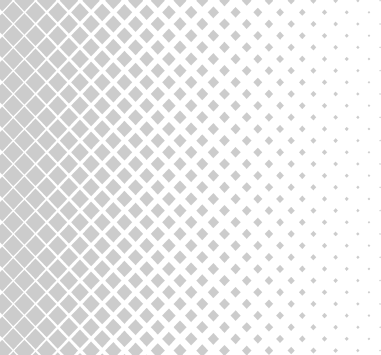
The Challenge: In a Word, PEEK
Spinal implants had been changed by another industry leader within the last decade. The traditional implant material, PEEK, was quickly being replaced by 3D printed interbody products made of polymer plastic. PEEK is very costly, because it’s controlled largely by the FDA which drives up the raw material costs.
CoreLink Surgical’s design team is always under significant pressure to keep pace with the changing tides in the industry. However, beyond that, the team was investigating the latest benefits that 3D printing could offer in designing materials and implants that match the strength and nature of actual bone.
To achieve this, they sought the support of third-party partners who would not only consult, but also introduce those technologies to CoreLink, enabling them to produce those materials in house, keeping in line with their business model.
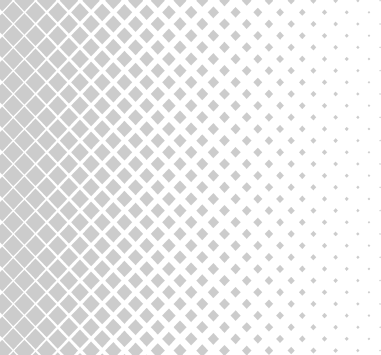
The Solution: Mimetic 3D Materials That Actually Imitate the Body’s Natural Materials
Hartwig and EOS have the consultative capacity to introduce our clients and partners to innovative solutions. In addition to providing training for the equipment we provide, our team can advise on materials, processes, and equipment selection to suit specific applications within a range of industries, including medical (where additive manufacturing is quickly becoming more widely adopted).
With CoreLink, this spoke to the mission of not only producing more efficient and technologically advanced production techniques. It also meant vastly improving the success rates of implant procedures, increasing the quality of life and pain management for the patients who receive their life-changing implants.
Hartwig introduced CoreLink to the additive team at EOS, and the result is a game-changing 3D-printed patented technology, Mimetic Metal®, a simulated implant material that:
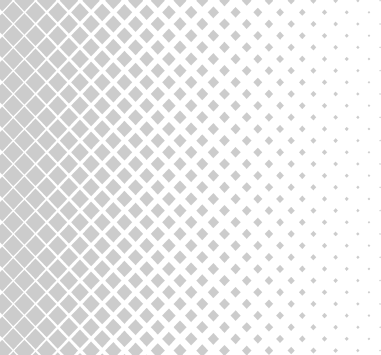
The Results: Lifesaving, Time Saving, and Game-Changing Implants
The resulting implant features an open-pore design to mimic a more bone-like strength and further reduce multi-directional strain. The open-pore design allows for enhanced and improved blood flow for improved mobility, faster healing, and better quality of life for the patient.
It all starts with R&D and lifelike digital prototypes. EOS’s CAD functionality allows improved simulations to determine just how the implant will react in various real-life scenarios, cutting down on the cost of R&D significantly. Sophisticated and highly precise color coding recreates that stress process before a prototype is created, further helping to reproduce the self-adapting properties of natural bone.
The titanium build plates are created right in-house by a 3-D technician, keeping all of their development not just local, but right on the factory floor. This process further reduces waste, part cost, secondary waste, and production time, namely since those parts require very little modification (wire EDMs, blades) or secondary hand finishing.
The reduction in the need for secondary processing keeps the parts more sterile during production, a vital advantage for surgical implants.
While ROI wasn’t their main driver, CoreLink was able to recoup the cost of equipment expenditures within a year. More than that, additive manufacturing developed an entirely new level of expertise for their products, further fulfilling their mission to heal and help patients.
Mimetic Metal would simply not be possible with traditional manufacturing methods.
Additive manufacturing solutions respond to the dynamics and complexities of their builds, allowing for the more custom nature of medical devices. Spinal implant kits could include 100 different SKUs, and most builds have at least six different lots per build. They’re able to keep their staffing levels minimal to enjoy this level of product diversity with limited run time. In a traditional machining scenario, this level of production would require 4 7-day 24-hour shifts (instead of 120 hour combined work weeks with 3D printing).
EOS machines are now used in daily operations at CoreLink Surgical. The additional advantages that they’ve enjoyed with EOS and Hartwig include consultative technological advice from the Additive Minds global team, as well as reliable, proactive support on all the machines they have in the shop.
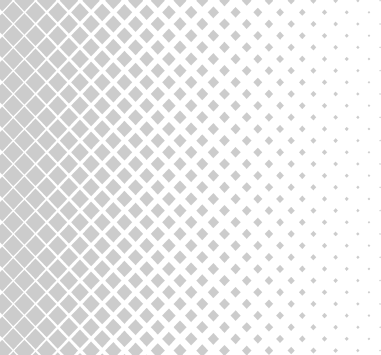
EOS and Hartwig Are Leading the Way in Additive Technology
“We prepare companies to innovate beyond existing boundaries with additive manufacturing. More than 400 successful customer projects show that Additive Minds can take your company to the next level,” says Thomas Weitlaner, Director of Additive Minds & Business Development EOS GmbH.
Together, Hartwig and EOS can help manufacturing leaders identify opportunities for implementing additive technology to fuel growth. The EOS Additive Minds team offers additional consultative expertise to help manufacturers determine and test the effectiveness of additive for specific applications.
For more information about how Hartwig can help introduce game-changing additive solutions to your floor and product suite, get in touch with our team of experts.
Ready to talk with a machine tool expert?
Your Hartwig representative can help connect you with the solution that will power your business’s next big innovation and efficiency.